3D Science Valley Insights
The Materials Genome Initiative generates vast amounts of materials data through high-throughput computation and experiments, providing rich training material for artificial intelligence. For instance, high-throughput computation can predict the structure and properties of materials, while high-throughput experiments can validate these predictions and generate actual performance data. Machine learning can uncover implicit relationships between material structure and properties from massive datasets. The deep integration of the Materials Genome Initiative with artificial intelligence can significantly accelerate the development process of new materials, shorten research and development cycles, reduce costs, and promote rapid advancements in materials science and engineering.”
Introduction: Professor Zhu Qiang’s team from the Department of Mechanical and Energy Engineering at Southern University of Science and Technology, in collaboration with Associate Professor Hu Xiaogang from Sun Yat-sen University, has made significant progress in the creep mechanism and performance prediction of laser-additive-manufactured high-crack-sensitivity high-temperature alloys. Their findings were published in the international journal Materials Science and Engineering: R under the title “Creep behaviour investigation of additively manufactured IN738LC superalloy based on Materials Genome approach”.

Laser additive manufacturing releases constraints in structural design and cross-scale organizational construction, providing innovative solutions to break through the manufacturing limits of current high-temperature structural materials, thereby meeting the urgent needs of major equipment such as aircraft engines and gas turbines for extreme high-temperature performance. Creep performance is a critical indicator for assessing the service performance and reliability of components in high-temperature environments, and its importance is self-evident. Therefore, accelerating the establishment of a creep performance database for laser additive manufacturing alloys and developing advanced creep behavior prediction technologies are of great significance in promoting the application of additive manufacturing technologies in equipment manufacturing.
However, high-temperature alloys produced by laser additive manufacturing currently face numerous challenges: first, high-performance high-temperature alloys are highly crack-sensitive, and cracking is a common issue during the printing process; second, the creep performance of laser additive high-temperature alloys is significantly lower than that of traditional cast alloys, limiting their potential for replacement under high-temperature and high-stress service conditions; third, traditional creep testing methods are inefficient and costly, making it difficult to meet the urgent demand for quickly establishing a database of relationships between material composition, manufacturing processes, and creep performance; fourth, existing creep performance prediction technologies mostly focus on predicting fracture life and lack accurate descriptions of the dynamic evolution of deformation and damage of materials at different service stages.
To address this challenge, Professor Zhu Qiang’s team and Hu Xiaogang have conducted collaborative research. The team used the high-crack-sensitivity high-temperature alloy IN738LC as a verification material and proposed a liquid-phase induced healing post-treatment scheme to repair micro-cracks generated during the laser additive manufacturing process, enhancing material density (Figure 1); based on this, the team developed a high-throughput creep testing technology that improves data acquisition efficiency by eight times while ensuring consistent compression creep temperature and load (Figure 2). The results show that after LIH treatment, the minimum compressive creep rate of the alloy is comparable to or better than that of many representative high-creep-performance engineering alloys (cast state) (Figure 3); furthermore, the team established a mapping relationship between the minimum creep rate and temperature and pressure based on optimization algorithms; finally, by integrating deep learning technology, they constructed a predictive model capable of accurately predicting the creep behavior of IN738LC alloys under any temperature and stress conditions, providing a powerful tool for assessing and optimizing the service performance of materials (Figure 4).
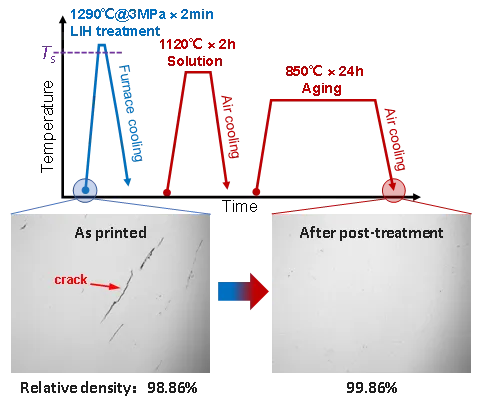
Figure 1. Repairing cracks in laser additive manufacturing using liquid-phase induced healing technology (LIH)
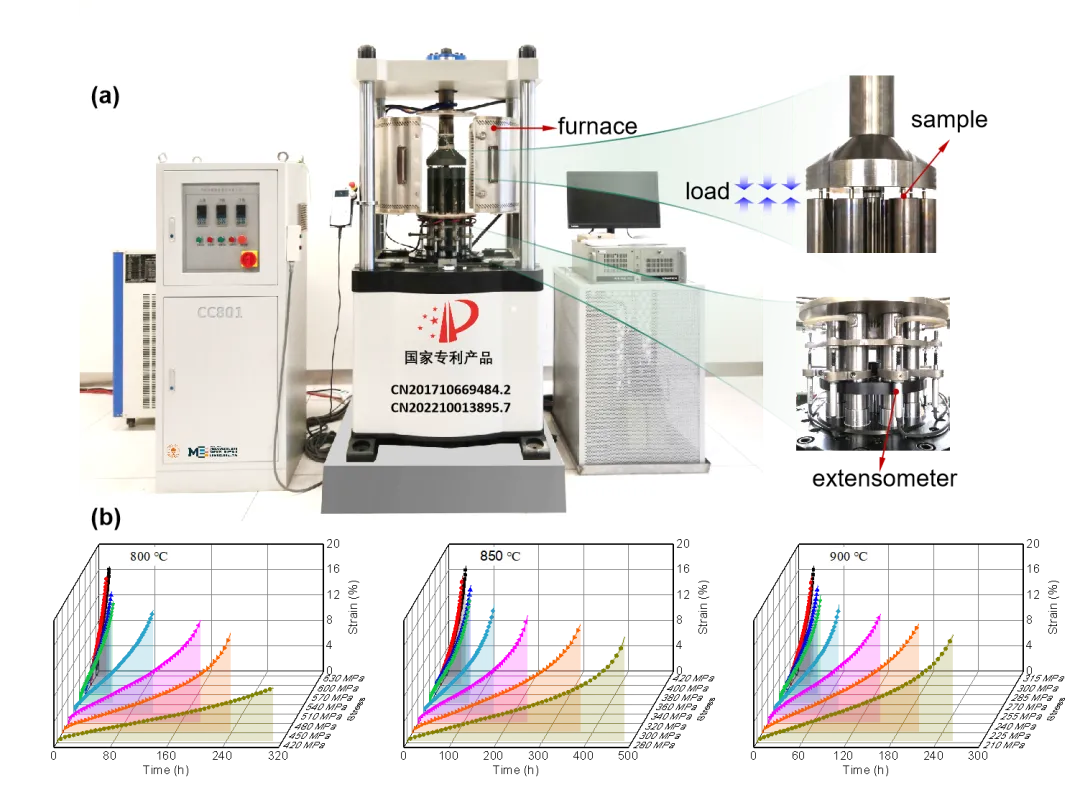
Figure 2. (a) High-throughput compressive creep testing system CC801; (b) Compressive creep curves of IN738LC under different temperature and stress conditions
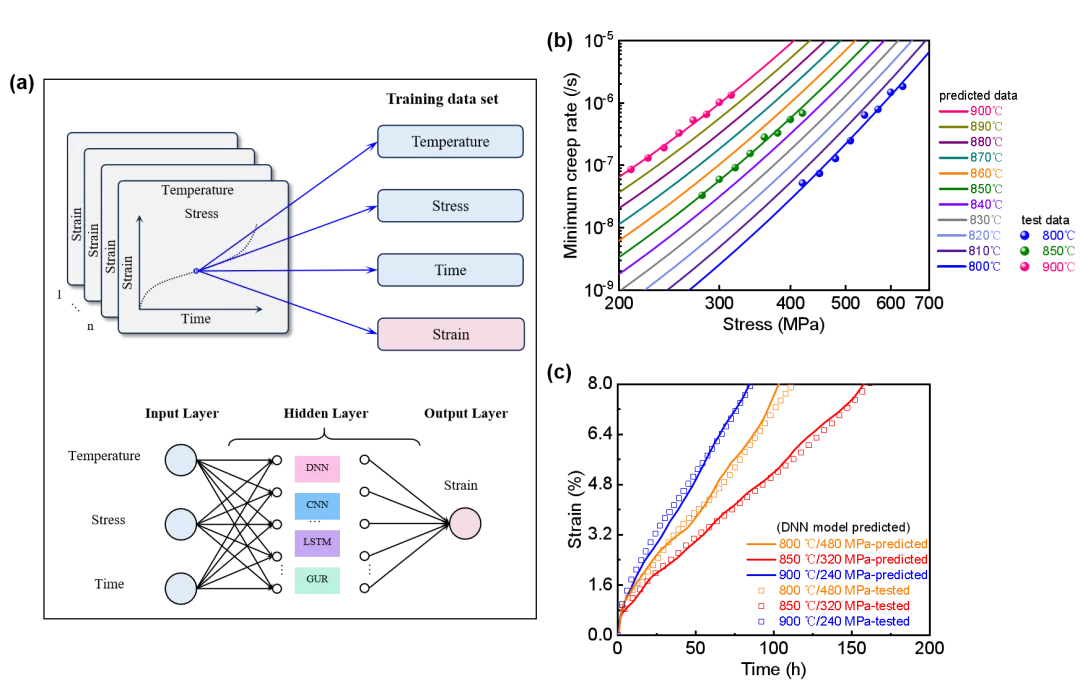
Figure 3. Comparison of minimum compressive creep rates between LPBF-IN738LC alloy (LIH treated) and commonly used high-performance high-temperature alloys (cast state)
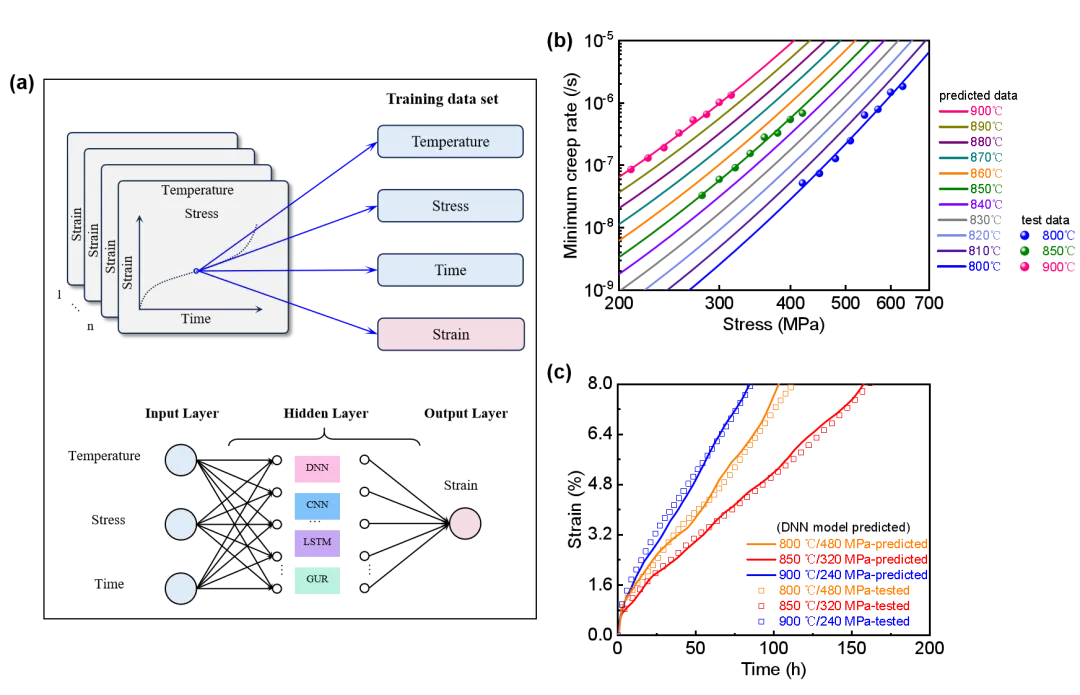
Figure 4. Prediction of LPBF-IN738LC creep behavior using deep learning models
This research not only utilizes laser additive manufacturing to produce high-crack-sensitivity high-temperature alloys with excellent creep performance and deeply analyzes their micro-mechanisms, but more importantly, it integrates high-throughput creep testing technology with machine learning based on the concept of the “Materials Genome Initiative”, providing a new pathway for establishing accurate creep behavior prediction models. This is of great significance for promoting the rapid development and widespread application of high-temperature structural materials.
Postdoctoral Xu Zhen from the Department of Mechanical and Energy Engineering at Southern University of Science and Technology is the first author of the article, with Zhu Qiang as the corresponding author and Hu Xiaogang as the co-corresponding author. Team members Dr. Lv Zhiwei, Wang Zhiyuan, Li Zhuoyu, Shi Zhifang, Chen Zhenan, and Associate Professor Guo Chuan from Sun Yat-sen University also made important contributions to the research. This study was strongly supported by the National Natural Science Foundation of China, the China Postdoctoral Science Foundation, the Shenzhen Science and Technology Innovation Commission, and the Analytical Testing Center of Southern University of Science and Technology.
Materials Science Network l Zhu Qiang’s team from Southern University of Science and Technology achieves significant progress in the study of creep behavior of additive manufactured high-temperature alloys