Ultrasonic transducers have been widely used in object detection, non-destructive testing (NDT), biomedical imaging, and therapy. Compared to bulk ultrasonic transducers, piezoelectric micromachined ultrasonic transducers (PMUTs) with a small footprint have advantages such as low power consumption and wide bandwidth, making them suitable for various applications in consumer electronics and the Internet of Things (IoT), such as Time-of-Flight (ToF) ranging, gesture recognition, fingerprint sensing, and 3D imaging. However, the relatively low output sound pressure of these small PMUT sensors limits their signal transmission in various applications. To expand the use of PMUTs in fields like haptic feedback, speakers, and acoustic tweezers, the main challenge is to achieve high sound pressure level (SPL) output.
The emission characteristics of PMUTs are mainly determined by their mechanical structure design and active piezoelectric materials, leading to an increasing demand for new materials in pursuit of higher performance.
According to MEMS Consulting, a team of researchers from institutions including the University of California, Berkeley, Southeast University, and Xi’an Jiaotong University has proposed an air-coupled PMUT based on sputtered potassium sodium niobate K0.34Na0.66NbO3 (KNN) thin films, which exhibits high sound pressure level output at low driving voltages. Test results indicate that a single KNN PMUT prototype has a resonant frequency of 106.3 kHz when driven at 4 Vp-p and demonstrates the following excellent characteristics: (1) large amplitude of 3.74 μm/V at voltage; (2) high acoustic RMS sound pressure level of 105.5 dB/V at a distance of 10 cm, which is 5-10 times higher than similar frequency PMUTs based on aluminum nitride (AlN). To highlight the advantages of this high sound pressure KNN PMUT, the researchers showcased its potential applications in haptic feedback, speakers, and rangefinders. Specifically, (1) a 15 × 15 KNN PMUT array generates haptic stimulation at frequencies within human perception range using pulse width modulation (PWM); (2) a single PMUT is tested as a speaker using amplitude modulation (AM) scheme with the resonant frequency close to the audible range; (3) a single PMUT is used as an onboard rangefinder based on pulse-echo measurements, demonstrating good transceiver capabilities. Therefore, this novel PMUT with high sound pressure level and low driving voltage can further extend to other applications requiring high sound pressure and miniaturized designs. The above research results were published in Microsystems & Nanoengineering under the title “High sound pressure piezoelectric micromachined ultrasonic transducers using sputtered potassium sodium niobate”.
PMUTs convert electrical excitation signals into sound waves through “electromechanical-acoustic” coupling. As shown in Figure 1a, the working diaphragm typically consists of a piezoelectric layer and a elastic layer, known as a unimorph diaphragm. When an external electric field is applied to the diaphragm, the piezoelectric layer generates in-plane strain through the inverse piezoelectric effect. The elastic layer displaces the neutral plane of the stacked structure away from the mid-plane of the piezoelectric layer, generating a bending moment that causes the diaphragm to undergo out-of-plane displacement. When an alternating current (AC) voltage is applied, the diaphragm vibrates periodically in the transverse direction, known as the flexural mode. This mechanical vibration drives surrounding medium particles to vibrate, ultimately emitting sound waves into the environment.
Figure 1 Structure and manufacturing process of KNN PMUT
The manufacturing process flow of KNN PMUT is illustrated in Figure 1c: (i) deposit the bottom electrode and KNN thin film on silicon-on-insulator (SOI) wafer; (ii) deposit and pattern the top electrode; (iii) etch the KNN thin film to form vias; (iv) form an oxide hard mask and bond to the handle wafer; (v) back-etch Si, using the embedded oxide as the etch stop; (vi) remove the handle wafer and oxide layer.
The researchers characterized the manufactured KNN PMUT, and the results are shown in Figure 2. Figure 2a displays the detection of the crystal structure of the sputtered KNN thin film using X-ray diffraction (XRD). Figure 2b shows the back images of PMUT devices with different aperture sizes, demonstrating the flexibility in designing and manufacturing devices with different resonant frequencies. The optical top view in Figure 2c highlights the good surface morphology of the PMUT. The cross-sectional scanning electron microscope (SEM) images in Figure 2d-f show clear back silicon cavities, tightly stacked Pt/RuO2/KNN/Pt/ZnO/SiO2/Si multilayer diaphragm structure, and the thickness of each layer (1.9 μm thick KNN and 5.2 μm thick Si device layer).
Figure 2 Characterization results of KNN PMUT
Next, the researchers conducted studies on the electrical, mechanical, and acoustic properties of the manufactured KNN PMUT, and the results are shown in Figure 3.
Figure 3 Electrical, mechanical and acoustic properties of KNN PMUT
Haptic interfaces can provide tactile feedback by stimulating mechanoreceptors located beneath the skin, enriching human-computer interaction. In recent years, airborne haptic stimulation has gained attention due to its rapid actuation, fine spatiotemporal resolution, and insensitivity to variations in skin surface. However, non-contact haptic systems based on bulk ultrasonic transducers have very large form factors (widths reaching several tens of centimeters), making them unsuitable for handheld or wearable applications.
The researchers proposed an airborne haptic interface device composed of a 15 × 15 KNN PMUT array. As shown in Figure 4a, the ultrasound generated by the PMUT array propagates through the air and causes vibrations on mechanoreceptors at the air-skin interface, generating tactile perception. The PMUT array prototype covers a total area of 2 cm × 2 cm, and acoustic pressure field assessments show that the natural focal point of the array, without beam focusing, is about 15 mm away from the diaphragm surface (as shown in Figure 4b). The emitted ultrasound is modulated into low-frequency signals using a pulse width modulation scheme, as mechanoreceptors cannot perceive ultrasonic frequency signals. Figure 4c shows the excitation signal, with a carrier frequency of 92.4 kHz, corresponding to the resonant frequency of the PMUT array. This signal is modulated to 200 Hz, which is within the frequency range where mechanoreceptors are more sensitive. The emission performance of the KNN PMUT was analyzed at different voltages, and the results are summarized in Figure 4d.
Figure 4 Performance evaluation of KNN PMUT array as a haptic actuator
Moreover, at a driving voltage of only 12 Vp-p, the emission sensitivity of the KNN PMUT is 120.8 Pa/cm²/V, at least twice that of AlN PMUTs at similar frequencies. Since the pressure achieved exceeds the minimum perception threshold of 1 kPa, 90% of volunteers achieved immediate non-contact haptic stimulation during the tests, experiencing a tactile sensation similar to wind.
Finally, the researchers also conducted performance evaluations of a single KNN PMUT as a speaker and onboard rangefinder.
In summary, this research proposed a PMUT based on sputtered KNN, where the KNN thin film exhibits good crystal quality with a high piezoelectric coefficient in the 001 orientation. The emission performance was evaluated using a single KNN PMUT (with a resonant frequency of 106.3 kHz at 4 Vp-p) and achieved a large amplitude of up to 3.74 μm/V and a velocity of 2.52 m/s/V. Thanks to the high surface velocity, an output sound pressure of 132.3 dB SPL was obtained at an axial distance of 1 cm, reaching 111.6 dB SPL at an axial distance of 10 cm. The corresponding emission sensitivity is 5-10 times higher than that of the state-of-the-art AlN-based PMUT. Its potential applications include acoustic cooling, portable and wearable ultrasound imaging, cardiovascular and edema monitoring, intravascular ultrasound imaging (IVUS), extracorporeal and interstitial high-intensity focused ultrasound (HIFU), non-destructive testing, flow meters, underwater imaging, particle manipulation, and acoustic tweezers.
Future research directions may include: enhancing multi-domain coupling effects and extending bandwidth through structural design, optimizing packaging design to improve acoustic coupling with the environment, developing customized electronic devices to enhance driving efficiency, and conducting studies on environmental sensitivity and long-term reliability for practical applications.
Paper link:https://doi.org/10.1038/s41378-024-00841-y
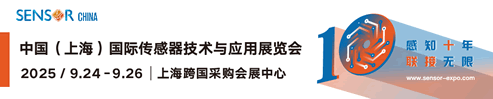