Electromagnetic Metallurgy Process Expert System (EPMVIEW5.0)
— Total word count: 8669 words, reading time: 19 minutes
1、EPMVIEW Overview
The strengthening of steel materials is the main development direction of steel products. The ways to improve the strength of steel materials mainly include: solid solution strengthening by dissolving alloying elements and interstitial atoms into the matrix structure; work hardening by increasing dislocation density through deformation; grain refinement which hinders dislocation movement across grain boundaries, resulting in fine-grain strengthening; and strengthening due to the precipitation of a second phase (generally Mx(C,N)y). Fine-grain strengthening is the most significant strengthening mechanism, and it is the only mechanism that increases both strength and toughness simultaneously. Due to segregation in steel (especially macro segregation such as central segregation), the uneven distribution of chemical composition causes heterogeneous properties in different parts of the steel, leading to inconsistencies in batch, specifications, and quality. The strengthening of steel materials requires high homogeneity in steel. Continuous casting is the first step in the production of steel materials. The focus of high-quality continuous casting work is on the high efficiency, high-end, and homogenization of fine-grain cast billets production. The continuous casting process is a battle against heterogeneity and casting defects, and it is a highly technical process. The stable control and homogenization of casting billet quality is a perpetual theme of continuous casting technology. The surface quality and internal homogenization of continuous casting billets determine the performance and use of the rolled products; the flow, heat transfer, solidification, and crystallization processes of molten steel during continuous casting, as well as the evolution and regulation of the solidification microstructure under external force fields, are key to improving casting machine productivity and stabilizing casting billet quality control. The stable control of the surface quality and internal microstructure of casting billets is a focus for steel enterprises. Through forward material design, precise process window stability control, and applying external force fields during the continuous casting process, the solidification and crystallization process of molten steel can be improved, thus stabilizing the internal quality of steel products, developing high-end products, and occupying the high-end steel market, which is a practical and efficient approach. Electromagnetic metallurgy is the foundation for the solidification of ultrafine-grain steel. The Lorentz force from the electromagnetic induction phenomenon acts on the flow and solidification crystallization process of the molten steel, converting electrical energy into kinetic energy of the molten steel without contact through the electromagnetic field. This force acts on the microstructure, ensuring the homogeneity of the casting billets, improving the solute uniformity distribution, and enhancing the axial and fine-grain structure. Its advantages include five high characteristics: high energy density, high cleanliness, high reliability, high controllability, and high automation. The electromagnetic metallurgy process and equipment for continuous casting are commonly used methods to improve micro segregation by applying non-contact external fields to the dendrite arms, improving the distribution of elements and second-phase particles in the steel at the microscopic structural scale, controlling the fluctuations of nucleation energy at the solidification front, and enhancing the morphology of primary grain boundaries, thereby forming sub-grain boundaries. Compared to mechanical pressing, which cannot effectively control segregation perpendicular to the pressing direction (lateral or slab width direction), electromagnetic force has a very good improvement effect. Through electromagnetic metallurgy process models and industrial software, the electromagnetic field and mechanical force fields can be systematically integrated for joint application in casting machines. This achieves the online optimization of casting organization under various steel grades and continuous casting conditions through the combined use of macro mechanical pressing stress and micro electromagnetic thrust, providing a reliable engineering implementation path for stabilizing and controlling the nucleation process and solidification microstructure of continuous casting billets.
Figure 1 Application of Electromagnetic Metallurgy Technology
Figure 2 Metallurgical Effects of Electromagnetic Metallurgy Technology
Figure 3 Application Areas of Electromagnetic Material Technology in High-End Material Preparation
2、Introduction of EPMVIEW Electromagnetic Metallurgy Process Expert System
Currently, EPM has been widely applied in the production fields of ferrous and non-ferrous metals (aluminum and magnesium materials), and its metallurgical effects have been recognized by domestic and foreign manufacturers. The advantages of electromagnetic metallurgy technology are obvious, and the manufacturing level of hardware equipment is continuously improving, paving the way for the application of electromagnetic metallurgy technology. However, having advanced equipment alone is far from sufficient; there is still much work to be done regarding how to stabilize and leverage the advantages of electromagnetic metallurgy process equipment under industrial production conditions in steel enterprises, with the following pain points:
Figure 4 Background of the Dynamic Precision Measurement and Control System of Continuous Casting Electromagnetic Metallurgy Process
The dynamic precision measurement and control system for electromagnetic metallurgy processes is a standard networked C/S architecture; the user interface is friendly and simple, achieving “one-click” intelligent control. The modular design concept gives the system a high degree of universality and portability. Industrial communication adopts a fully digital solution based on TCP/IP protocol, with large data throughput, strong anti-interference ability, and high real-time performance. The system adopts a redundant safety design concept, and in case of emergency situations on-site, the system can automatically interrupt the equipment. At the same time, production operators have absolute priority to interrupt the continuous casting electromagnetic metallurgy equipment, fully ensuring the safety and efficiency of system operation.
Figure 5 Basic Principles of Electromagnetic Metallurgy
Figure 6A Background of the Dynamic Precision Measurement and Control System for Electromagnetic Metallurgy Process
The dynamic precision measurement and control system for electromagnetic metallurgy processes integrates complex electromagnetic metallurgy processes into a computer control system, representing a typical high-end industrial process control system. The system utilizes a multi-bus network duplex data communication system that is compatible with continuous casting machines and electromagnetic metallurgy hardware from multiple manufacturers, achieving seamless integration with the continuous casting machine system. The electromagnetic metallurgy parameters are intelligently and dynamically controlled based on the continuous casting conditions captured through the EPMVIEW model.
EPMVIEW System Code | System Name | Applicable Field |
DEP-EPM-CCFC5.1.3 | Intelligent Control System for Electromagnetic Braking of Conventional Slab Continuous Casting Crystallizers |
Applicable to conventional slab continuous casting process, dynamic argon blowing balance module,dynamic magnetic control flow |
DEP-EPM-CCEC5.1.6 | CSP-ESP Slab Continuous Casting Crystallizer Electromagnetic Braking Intelligent Control System |
Applicable to CSP and ESP slab continuous casting processes,dynamic argon blowing balance module |
DEP-EPM-CCSS5.1.9 | General Intelligent Control System for Slab Continuous Casting Fan-Shaped Segment Electromagnetic Stirring |
General slab continuous casting process, dynamic magnetic control crystallization function |
DEP-EPM-CCSM5.0.3 | Intelligent Control System for Electromagnetic Stirring of Slab Continuous Casting Crystallizers |
Applicable to conventional slab continuous casting process, dynamic argon blowing balance module |
DEP-EPM-CCBM5.2.5 | Intelligent Control System for Electromagnetic Stirring of Square and Round Billet Continuous Casting Crystallizers |
Applicable to steel and non-ferrous metal fields ,dynamic argon blowing balance module |
DEP-EPM-CCBS5.1.6 | Intelligent Control System for Electromagnetic Stirring of Square and Round Billet Continuous Casting Secondary Cooling Segments |
Applicable to steel and non-ferrous metal fieldsdynamic magnetic control crystallization function |
DEP-EPM-CCBF5.1.6 | Intelligent Control System for Electromagnetic Stirring of Square and Round Billet Continuous Casting Solidification End | Applicable to steel and non-ferrous metal fieldsdynamic magnetic control crystallization function |
DEP-ICS-INCIC2.1.6 | Industrial Intelligent Data Router (Network Duplex 10ms) | Standard configuration for DEPVIEW systemdistributed networkreal-time duplex communication |
*Function description of the continuous casting electromagnetic metallurgy process expert system version:
1)EPMVIEW5.3.1.***B, basic process version, electromagnetic metallurgy process model
2)EPMVIEW5.3.1.***P, vector magnetic field version, electromagnetic metallurgy process model + MPO vector magnetic field,
3)EPMVIEW5.3.1.***M, material process version, electromagnetic metallurgy process model + MPO vector magnetic field module + high-temperature materials science module.
Table 1 Selection of Continuous Casting Electromagnetic Metallurgy Process Expert System
Figure 6B Some Engineering Applications of Electromagnetic Metallurgy Process Expert System HMI Interface
3、Composition of EPMVIEW Subsystems and Metallurgical Effects
1、About EPMVIEW5.0 System and Some Engineering Application Scenarios
Figure 7 Based on DEP-DADCS Distributed Network Real-Time Measurement and Control System Architecture Online Measurement and Control System
Figure 8 Integration of Digital Duplex Measurement and Control Data Communication System and Precision Measurement and Control System for Metallurgical Models
Figure 9 Dynamic Magnetic Control Flow of DEP-EPMVIEW5.0 Crystallizer Subsystem
Figure 10 Dynamic Magnetic Control Flow and Electromagnetic Purification of DEP-EPMVIEW5.0
Figure 11 Solidification Process Magnetic Control Crystallization of DEP-EPMVIEW Subsystem
Figure 12 Magnetic Control Crystallization Subsystem of DEP-EPMVIEW
2、Metallurgical Effects of DEP-EPMVIEW5.0
Length/mm | Diameter/mm | Yield Strength/N | Tensile Strength/N | Yield Strength/Mpa | Tensile Strength/Mpa | Cross-Sectional Contraction Rate /% | |
EPMVIEWElectromagnetic Metallurgy |
50 |
10.03 |
78750 |
91700 |
995 |
1160 |
64.0 |
Conventional Electromagnetic Metallurgy |
50 |
10.04 |
76400 |
85650 |
965 |
1080 |
68.5 |
Figure 13 Improvement of Equiaxed Crystal Rate in Continuous Casting Billets
Figure 14 Improvement of Central Segregation in Continuous Casting Billets
Figure 15 Magnetic Control Crystallization Organization Structure Optimization (Top image is slab, bottom image is square billet)
Figure 16 Improvement of Magnetic Control Crystallization in EPMVIEW5.0
Figure 17 Improvement of Internal Quality of Casting Billets through Magnetic Control Flow and Electromagnetic Purification
4、Typical Application Scenarios of EPMVIEW5.0 System
1. Online Control of Solidification Structure of High-Grade Electrical Steel
High-grade electrical silicon steel plays a very important role in the development of the national economy and national energy strategy. High magnetic orientation electrical steel and high-grade non-oriented electrical steel are widely used in large transformers, large generators, electric motors, and household appliances, such as the Xiaolangdi Project, Three Gorges Project, Qinghai-Tibet Railway Project, Beijing positron collider project, Shenzhou VI and VII manned spacecraft projects, high-speed rail, robots, new energy vehicles, and other national key projects and fields. Before 2008, a certain share still needed to be imported. However, from 2017, the proportion of top-end products in China’s high-end electrical steel output is not high, and user demand cannot be fully met; the production control level needs to be improved, and the qualification rate of original grades must be increased, reducing the number of defective products or products with defects, and improving management levels and overall product quality. Facing new demands from downstream industries such as large domestic power generation equipment, energy-saving transformers, high-efficiency energy-saving motors, transportation drive motors, new energy electric vehicle motors, drones, and high-end household appliances, the preparation technology for low-noise transformer-oriented electrical steel, heat-resistant oriented electrical steel for three-dimensional rolled iron cores, thin non-oriented electrical steel, high-end efficient non-oriented electrical steel, mid-frequency efficient non-oriented electrical steel, and high-strength non-oriented electrical steel should be prioritized for development. The initial solidification structure is a guarantee for the formation of the target texture of finished products and one of the factors affecting the magnetic induction strength B25 and B50 of electrical steel. The ideal non-oriented crystalline texture is (100) face texture, isotropic, and the hard magnetization direction [111] is not on the rolling surface; the magnetic induction strength of oriented silicon steel only relates to the (110)[001] grain orientation or (110)[001] orientation deviation angle. To improve the magnetic performance of electrical steel, applying optimized online magnetic field control of the solidification structure during production to promote the formation of favorable textures has become one of the key core technologies.
2. Online Optimization of Solidification Structure of Continuous Casting Billets under Composite Stress Fields
In the foreseeable future, steel products will still be the preferred or necessary materials for economic construction and development. Thick plate products hold an important position and wide applications in national economic development and military industry. The internal quality issues of continuous casting billets restrict the development of high-end thick plate products. Due to the large thickness of finished plate products and the small rolling compression ratio, the central porosity and central segregation of continuous casting billets are the main sources of quality defects in thick plate products. Therefore, effectively suppressing central segregation, central porosity, and elemental segregation is key to achieving homogenization and high-quality casting billets in continuous casting production, which is the origin and core of high-end thick plate products. Low-carbon equivalent alloy steel grades in high-end thick plates are widely used in engineering due to their excellent weldability. However, the segregation of alloying elements is not limited to C and S elements. The degree of segregation of strengthening alloying elements is much higher than that of carbon and sulfur segregation, and its harm is also much greater than that of carbon and sulfur segregation. The segregation of alloying elements is not easily captured or detected through conventional low-magnification detection and is easily overlooked. However, the aggregation of alloying elements and high-temperature phase transition products is a major obstacle to the production of high-grade steel materials.
Effects of Alloying Elements in Steel and Their Segregation on Steel Properties
The segregation of large atomic weight alloying elements cannot be improved solely by macroscale mechanical stress, and must be considered from the perspective of initial crystallization and intermolecular forces. Electromagnetic thrust is currently considered a more ideal technology for effectively improving central segregation and elemental segregation, while mechanical pressing force is used to effectively control central porosity. In-depth research on the solidification process of liquid steel during continuous casting and the evolution and control of solidification microstructure under the external stress fields of light pressing mechanical pressure and electromagnetic field can provide a solid basis for stabilizing casting machine productivity and internal quality of casting billets, providing high-quality homogenized raw materials for upgrading steel products.
To achieve excellent internal quality of casting billets, it is necessary to control the surface temperature of casting billets in the continuous casting process to meet the solidification process requirements of steel grades. Dynamic secondary cooling is an online water distribution model composed of basic water quantity, control water quantity for target surface temperature of casting billets, and water quantity adjustment calculations. By collecting actual cooling circuit water flow, drawing speed, steel grade composition, and tundish steel water superheat to determine the online temperature distribution of the casting flow, corrections are made against the target surface temperature of the steel grades, ultimately setting up the water quantity values for each secondary cooling zone for the execution mechanism of the secondary cooling system. The main metallurgical functions of the system are: (1) dynamically distributing water in the secondary cooling circuit according to casting conditions (2) outputting the thermodynamic state of the casting billets and the liquid-solid phase ratio to the automatic control system for the casting billet taper and the electromagnetic metallurgy S-EMS system.
The strain ε generated by the mechanical stress field of light pressing on the casting billets is calculated by the following formula:
In the formula: c-constant/m·mm-1; δ: bulge amount mm; ɑ- shell thickness/m; l- roll distance/m.
When the shape change of the shell during fan-shaped segment pressing exceeds the allowable strain value of the shell, primary cracks occur in the solidified shell of continuous casting. Further pressing leads to internal cracks in the casting billets. The solidification front liquid-solid interface is a zero-strength brittle zone. The requirement for the pressing rate is: ε<ε0 (critical strain value of casting billets).
The allowable strain rate that a shell of a certain thickness can withstand for different steel grades is the limit pressing rate, and the deformation caused by the limit pressing rate cannot exceed the allowable strain critical value of the steel, otherwise pressing cracks will occur. The limit pressing rate for light pressing is calculated by the following formula:
In the formula: VR- pressing rate mm/min; D- thickness/mm; W- casting billet width/mm; TL- liquidus temperature/℃; TS- solidus temperature/℃; appropriate macro casting billet pressing stress and pressing rate can compensate for the shrinkage at the solidification end, breaking up dendritic bridges to improve the internal quality of casting billets.
In the secondary cooling segment or at the solidification end, applying a low-frequency electromagnetic field, the traveling wave electromagnetic field scans at a certain speed while the unsolidified liquid steel in the casting billet is cut by the externally applied alternating magnetic field at a considerable speed, inducing an electromotive force E. Since molten steel has electrical conductivity σ, the induced current can be calculated by the following formula:
The direction of the induced current is perpendicular to the direction of flow and the direction of the applied magnetic field, following the right-hand rule. This induced current interacts with the externally applied alternating magnetic field and the local induced magnetic field, generating electromagnetic thrust in the molten steel, calculated by the following formula.
Electromagnetic thrust is a volume force acting on the microscopic volume unit of the molten steel, using electromagnetic force to improve the flow, heat transfer, and migration processes during the solidification of molten steel, refining grains, and increasing the equiaxed crystal rate in casting billets. It improves the distribution of second-phase particles in steel and strictly controls composition segregation, expanding the range of steel grades produced. The online measurement and control system employs multiple model interlinked measurement and control to stably produce homogenized casting billets required for high-end thick plates, low alloy, medium carbon, high carbon, and ultra-high carbon grades.
Group Image 2 Magnetic Control Crystallization Improvement of Second-Phase Particle Distribution in High-End Thick Plate Steel
3. Control of Inclusions and Surface Quality of Hot-Rolled Ultra-Deep Drawing IF Steel, Automotive Steel, and High-Grade Pipeline Steel
The crystallizer is the first step in the phase transition of liquid steel to solid. The flow state, cooling heat transfer, and vibration parameters of molten steel in the crystallizer determine the morphology of the initial shell, the distribution of inclusions, and the degree of surface defects of casting billets. By optimizing the crystallizer vibration metallurgical process parameters model, reducing negative slip time, alleviating casting marks, and lowering the risk of initial cracks, the crystallizer’s flow control metallurgical process model rationally allocates the outflow of molten steel from the submerged entry nozzle in the crystallizer, not only suitable for low-carbon and ultra-low carbon steel series under high drawing speed conditions but also for low drawing speed conditions and high carbon and high alloy steel, applying its flow field optimization function. By reasonably controlling the flow field of the crystallizer, the liquid surface can be activated, increasing the temperature of the meniscus, forming a hot-top crystallizer, improving the uniformity of heat transfer in the initial shell, and reducing the sensitivity to cracking of the steel grades. By optimizing the electromagnetic force to break large inclusions, significantly promoting the upward movement of small-sized inclusions, further improving the cleanliness of casting billets, and applying it to produce automotive sheets, pipeline steel, and other high-grade steel grades with extremely high inclusion content requirements.
The application of crystallizer vibration parameter optimization and dynamic magnetic control flow control expert system has improved the versatility of continuous casting machines for drawing speeds and steel grades. The fluctuation of ultra-low carbon steel liquid level has been reduced from ±5mm to ±2mm, the uniformity of temperature in the crystallizer has improved by 60%, casting marks have been reduced by 1-3mm, and the consumption of protective slag has increased by 6% year-on-year; the T[O] value in casting billets has decreased by 41%, and the scrap rate of inclusions in cold-rolled products has decreased by one-third, resulting in significant economic benefits.
4. Process Optimization for High-Quality Bars and Wires, Non-Ferrous Metals, and Aerospace Aluminum and Magnesium Materials
Figure 18 Electromagnetic Metallurgy Measurement and Control System for Square and Round Billets
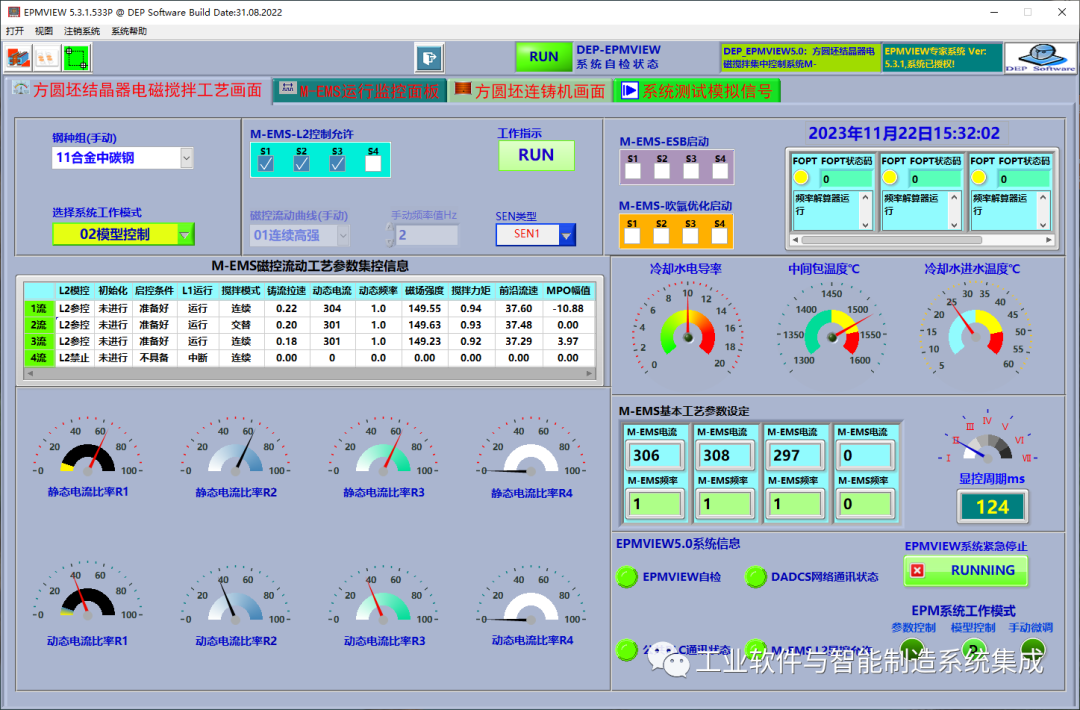
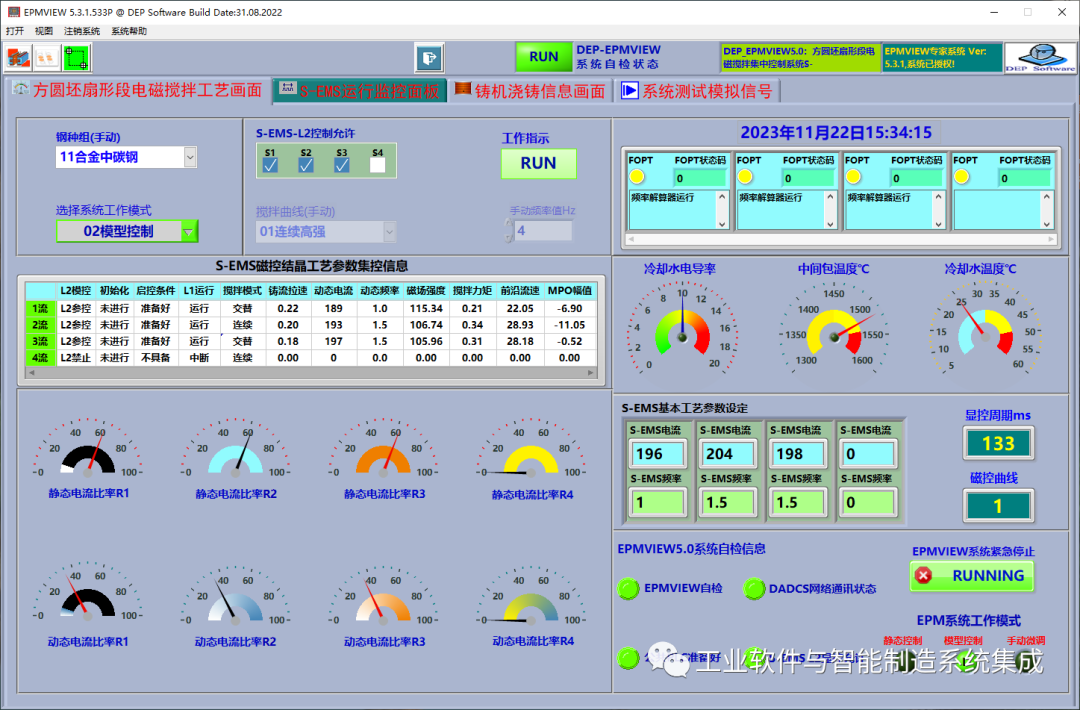
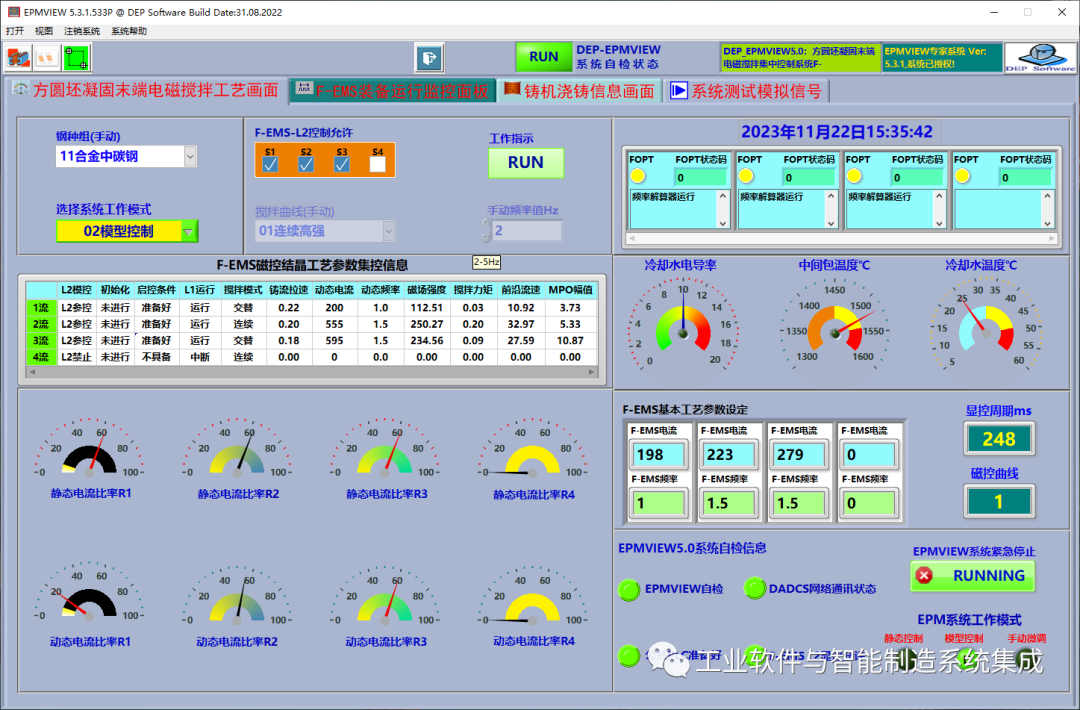
Figure 19 Precision Measurement and Complete Electromagnetic Metallurgy Process Expert System at the Solidification End of Square and Round Billets
Due to the characteristics of square and round billet equipment, the electromagnetic metallurgy process is one of the few, and sometimes even the only, quality control means for casting billets. When producing large round billets (800mm and above cross-section) for bearing steel, gear steel, and seamless pipes; and square billets for heavy rails, the online precision dynamic measurement and control system for electromagnetic metallurgy is a fully necessary core process measure when strict control of casting billet segregation and internal quality is required. Therefore, the online precision dynamic control model for electromagnetic metallurgy is essential for producing high-quality bars and wires, non-ferrous metals, aerospace aluminum and magnesium materials, and the solidification and forming processes of materials, magnetic control crystallization, and magnetic control flow to enhance the strength and toughness of the body.
5. High-Temperature Performance of Metal Materials and Electromagnetic Materials Process Package
Undertaking the results of forward research and design of digital materials to provide high-temperature thermal physical properties and entrance precision parameters for the continuous casting electromagnetic metallurgy process, allowing the application of electromagnetic force to be just right, neither too hot nor too cold.
Figure 20 CCMP-EPMVIEW5.0 High-Grade Metal Materials Cradle with Metal Materials Process Package
DEP-EPMVIEW5.0 Main Features:
1. The electromagnetic metallurgy process expert system implements customized digital dynamic electromagnetic metallurgy processes for continuous casting, steadily applied to continuous casting sites, achieving digital and modeled industrial production of continuous casting electromagnetic metallurgy processes. It precisely controls the energy fluctuations and crystal growth forms during the crystal growth process, equipped with a general industrial-grade intelligent brain for materials engineering process packages and continuous casting electromagnetic metallurgy processes and equipment. It achieves magnetic control fine crystallization, two-phase distribution and morphology control, homogenization of casting billets, and precise control of the magnetic control flow process during the solidification process. The solidification crystallization process is precisely controllable, and the homogenization of casting billets is mass-produced, ensuring the quality of rolled products.
2. The electromagnetic metallurgy process expert system mainly addresses the stability issues of electromagnetic metallurgy processes and product quality, providing mechanisms, equipment, processes, and quality guarantees for the production of homogenized casting billets, building core competitiveness for enterprises to meet challenges and improve quality and efficiency. Transitioning from one generation of equipment and materials to one generation of materials and equipment emphasizes the strategic role of materials. The system significantly reduces quality risks for variety steels, improves yield rates; stabilizes the quality of variety steels, forming the capability for bulk supply, and constructs core competitiveness in the high-end brand market.
3. The electromagnetic metallurgy process expert system serves as a bridge between continuous casting machines and electromagnetic metallurgy equipment. Through system integration, it realizes a complete set of continuous casting process solutions under the composite external field, effectively improving and stabilizing the segregation levels of carbon steels and alloy steels, achieving 3D homogenization of casting organization in the width, thickness, and casting length directions, providing high-quality raw materials for subsequent rolling. It lays a key technical foundation for the stable mass production of customized homogenized continuous casting billets required for high-end steel materials.
Figure 21 CCMP-EPMVIEW5.0 Advantages
1. The EPM metallurgy model provides precise electromagnetic metallurgy process parameters and electromagnetic stirring tangential forces for continuous casting machines.
2. MPO multi-phase vector magnetic field provides radial forces that traditional continuous casting electromagnetic metallurgy processes cannot offer, applying the electromagnetic clamping effect of magnetic flux changes to provide radial electromagnetic force components directed at the geometric center of the casting billets for various electromagnetic stirrers (AC power); providing electromagnetic screening and electromagnetic wave dynamics for the crystallizer electromagnetic brake (DC power) to promote the upward movement of small-sized inclusions and enhance heat transfer and slag protection in the crystallizer.
3. The continuous tangential and radial forces acting on the CET frontier jointly control the width of the bright band at the CET frontier. MPO enables controlled resonance of molten metals in closed cavities, promoting the uniform distribution of solutes in the solidification zone; magnetic-induced supercooling promotes the nucleation rate, achieving homogenization of the casting billets.
4. The radial electromagnetic force directed at the geometric center of the casting billets further refines the grains while providing the possibility to fully control the central porosity and shrinkage holes, achieving homogenization of the microstructure of the casting billets.
The electromagnetic metallurgy process expert system is the foundation for homogenized fine-grain casting billets, serving as a bridge that connects and deeply integrates electromagnetic metallurgy processes and equipment with continuous casting processes and equipment. Electromagnetic metallurgy equipment acts as a coupled servo system for continuous casting machines, dynamically and rapidly responding to changes in continuous casting processes; the integrated production technology of homogenized casting billets in continuous casting adjusts the relationship between electromagnetic force and argon blowing in real-time according to casting conditions, keeping the flow of steel liquid in the crystallizer in a stable process state to improve the surface quality of casting billets; the magnetic control crystallization model accurately coordinates and optimizes low-frequency electromagnetic force and mechanical pressing force in real-time to improve the internal quality of casting billets. The electromagnetic stirring and light pressing equipment in the fan-shaped section complement each other through dynamic solidification processes and electromagnetic metallurgy process models, dynamically adjusting the electromagnetic metallurgy equipment and pressing parameters to ensure a reasonable match and fully leverage their respective advantages. This realizes the evolution and improvement of the solidification and solid-state organization of casting billets under the combined effects of macro mechanical stress and micro electromagnetic thrust, providing mechanisms, equipment, processes, and quality guarantees for the production of high-end alloy materials for aerospace, low-carbon alloy ship plate steel, pipeline steel, and other easily segregated steel grades, laying a solid technical and practical foundation for the production of continuous casting billets with special high-quality requirements.
High-end steel materials call for high-end metallurgical processes and equipment. New materials and deep modification technologies for materials are strategic emerging industries and have become one of the most important and fastest-developing scientific and technological fields today. The transition from “one generation of equipment and one generation of materials” to “one generation of materials and one generation of equipment” highlights the strategic role of materials. The development of high-end materials technology can promote the formation and development of strategic emerging industries in our country. The deep integration of multi-field interactions, material electromagnetic fluid (MHD), and electromagnetic process technology, materials science and engineering, and modern measurement and control technology and systems will drive the upgrading of high-end material preparation technologies and product updates in traditional industries and pillar industries.