Source / “Cotton Textile Technology”
Authors / Zhao Yang, Li Guanghai, Xiao Qin, Wang Zhaoxu, Feng Wen
Editor / Cotton Textile Technology New Media – Cindy
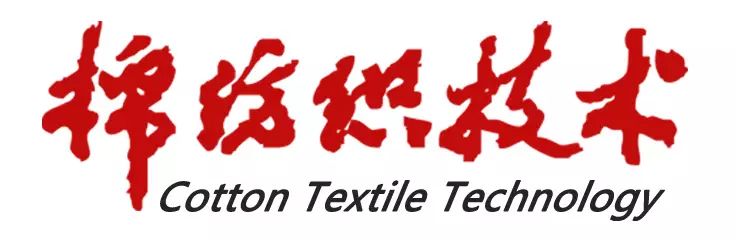
Original published in: December 2016
Volume 44 (Total Issue 542)
This article introduces the application effects of the USTER QUANTUM EXPERT 3 winding expert system. It elaborates on the main functions and process optimization methods of the USTER QUANTUM EXPERT 3 winding expert system, and analyzes its application effects in production, quality control, and equipment maintenance. It is believed that this expert system has a large data volume, comprehensive functions, and can not only perform real-time monitoring but also control processes and product quality, which helps identify abnormal issues in the production process and facilitates equipment maintenance and improvement of production efficiency.
winding; expert system; electronic clearing device; yarn body graph; yarn defects; quality monitoring
As the labor pressure increases in textile enterprises, it is urgent to reduce costs and improve labor productivity. Textile enterprises can only reduce labor intensity and improve labor productivity by adopting new technologies and new equipment, actively developing textile intelligence. Our company has used the USTER QUANTUM EXPERT 3 winding expert system, which connects all winding clearing devices, collects real-time settings and quality data from each clearing device, and stores all information in a database. The data is directly imported into terminal computers for easy data analysis, trend identification, and potential problem analysis, which not only reduces the cumbersome work of manually recording and counting data but also achieves comprehensive control over the winding process. Through the terminal computer, we can directly see various parameters of the winding machine, quickly understand the production status, and directly export summary data without the need for manual labor for data summarization and analysis. We can create and edit varieties and their process settings, download them to the machines through the expert system, facilitating changes and adjustments to production processes, and display the efficiency and current production status of each spindle. To facilitate understanding of winding efficiency, we display the data from the winding expert system in real-time on the workshop’s TV screen, allowing workshop managers to understand the real-time efficiency of winding promptly. The winding expert system achieves comprehensive online quality monitoring, especially with a simple and intuitive human-machine dialogue user interface, which guarantees effective control over yarn quality.
1 Main Functions of the USTER QUANTUM EXPERT 3 Winding Expert System
The expert system mainly covers four aspects: monitoring, reporting, varieties, and configuration.
Monitoring. This menu reflects the overview of machine production, displaying all winding machines that are connected to the system and configured. It specifically shows the clearing groups and their actual production status for each machine. Each variety corresponds to different colors. The monitoring content includes AEF (production efficiency), YF (yarn defects), YB (natural breaks), Prod (output), QA (quality alarms), YA (yarn defect alarms), JR (joint failure rate), YJ (yarn joints), and other information. As shown in Figure 1, the online efficiency of winding machine 11 is 82.9%.
Reporting. This menu contains a large amount of information, mainly organizing data into various reports through tables, charts, and drawings. It can be used as a filter for focusing on specific machine or variety report data; standard reports can be modified or custom reports can be created according to production needs; reports can be printed or saved as files; long-term quality chart trends and exceptions during the production process can be viewed.
Varieties. All available varieties connected to the server are displayed in this menu. A variety can be selected for comparison with other varieties, changing the clearing limits, and downloading them to the running machines. The clearing limits are visualized and clearly presented, allowing all information to be seen on one screen.
Configuration.. The CCU configuration is completed by the system through the configuration of the CCU to be connected, with communication addresses, clearing device types, etc.; general settings are used to define commonly used units for data reports; user/role configuration is used to set each user’s role and access level permissions. Shift settings define production shift times, storing production and quality data at the end of the shift; the limit editor is used to customize the limit ranges for production data, yarn defect cutting, alarms, and special cutting, which will be effective in various abnormal reports, with values above or below the limits displayed in red.
2 Applications of the Winding Expert System
2.1 Correct Naming of Production Varieties
During the production process, multiple varieties are generally produced simultaneously, with the same number having both single yarn and twisted yarn. Therefore, the naming and coding of varieties must be consistent, using a simple and convenient naming method for differentiation, which can help us analyze and organize reports for long-term reference, avoiding confusion. We stipulate that the variety name consists of the yarn number and the cotton blend code, and the variety code consists of the company name and the yarn number. For example, pure cotton 11.66 tex gathering spun single yarn, variety name CF50/1-CA, variety code XJE-5001; pure cotton 7.28 tex×2 gathering spun twisted yarn, variety name CF80/2-ZB, variety code XJE-8002. In this way, setting a variety in the expert system corresponds to a color, as shown in Figure 1, where winding machine 8 produced 3 varieties, with the pink variety produced in both winding machine 8 and winding machine 12, making it clear at a glance. Using simple and clear markings facilitates data storage and filtering, avoiding errors due to improper naming and providing a basis for correct downloading of processes.
2.2 Centralized Management of Variety Processes
Under the premise of meeting user quality, fine-tuning the clearing curve and downloading the adjusted process to different production machines is very convenient and quick, just like operating on the clearing device panel. For instance, if an over-standard situation is found after sampling the white fabric variety, the FD parameters can be adjusted through the expert system and downloaded to the corresponding production machine. The expert system also allows viewing of other process parameters for this variety, and if changes are needed, they can be directly set on the panel and downloaded to the machine. As shown in Figure 2, the variety management interface can globally control the setting of clearing limits, which is beneficial for optimizing process parameters and managing clearing parameters for all varieties of machines.
In Figure 2, the yarn body situation can be seen, which contains the expected and natural variations of normal yarn, representing the nominal yarn and its tolerances, i.e., the commonly occurring yarn defects. It shows the full picture of yarn characteristics. The yarn body consists of two parts: the deep green area represents the real yarn body, and the light green area represents the yarn body variation. In the yarn body graph, in addition to the two green areas, green dots represent retained defects in the yarn, and red dots represent harmful yarn defects that have been removed. In the expert system, built-in intelligent limits or clearing curve options can be used flexibly for setting and optimization; all production variety settings are stored centrally for easy retrieval and downloading in the future; previous similar variety settings can be quickly retrieved as a basis for changes to control varieties and settings. At the same time, detailed data on the number of defects cut and retained in the entire winding process can optimize the clearing curve of the clearing device. This optimization of the clearing curve, compared to single machine optimization, takes into account the entire production variety situation rather than just one winding machine, thus reducing a lot of unnecessary cuts while ensuring quality and improving winding efficiency.
In the expert system, the clearing curves of the same variety produced by different machines can be compared, and the comparison of clearing limits is a fast and effective method to check whether various settings are consistent throughout the production process. Combined with the yarn body comparison, the clearing limits can be fine-tuned, and it can be determined whether raw materials or process settings have changed. When significant differences between the yarn bodies of machines are found, the correct process parameters should not be modified lightly, and a defect analysis should be conducted on machines with high yarn defects to find the causes in previous processes.
2.3 Editing Custom Reports
The expert system has many reports related to output, equipment, speed, quality, alarms, and more. For convenience, specific reports can be created based on the content of interest, allowing all indicators of concern to be viewed in one report, and parameters can be set by oneself, with automatic prompts for quality alarms in the report, clearly displaying some exceeding indicators. The system’s limit reports can identify machines or machine groups with alarm limits exceeded. These reports can directly point out the root causes of problems, and through analysis of the causes, ultimately reduce the number of defective yarns, save production costs, and control the production process. The edited reports can be stored in custom reports.
2.4 Viewing and Controlling Exceptions
Expert system data volume is large, and through alarm settings, it can record textile alarms and quality alarm data, recording the number of alarmed yarns every day, as shown in Figure 3.
From Figure 3, it can be seen that the PC cutting set for CF80/2-AXB is quite high, and the number of alarms per shift is also over 100. We analyze the defects in the yarn through physical analysis, laboratory measurements, and fabric weaving, as shown in Figure 4.
From Figure 4, it can be seen that the yarn defect blackboard has obvious regularity. Therefore, strengthening the condition of the rubber rollers in the fine yarn process and checking the cleanliness work will change the cleaning from once per shift to twice per shift; the cleaning of the fluff rollers will change from every other day to daily. At the same time, strengthen the cleaning work in the drawing area, shortening the wiping cycle. Thus, based on the quality situation of the variety and the alarm status, timely adjustments to production control have been effectively guided.
2.5 Viewing Production Situations such as Shift Reports, Daily Reports, and Weekly Reports
By checking the shift reports daily, we can identify abnormal spindles, promptly repair broken spindles and those with low efficiency, and check the differences in table deviations to reduce yarn defects. Daily reports allow us to review abnormal and operational conditions across three shifts, checking cleaning and maintenance times and winding speeds. Weekly reports help us understand product quality and the cutting trends of yarn defects, as well as the production trends of each machine per shift. In Figure 5, the daily data from the expert system shows the cutting situation of the CF50-Cj white variety on different machines: under the same clearing parameter settings, the FD cutting difference between the two machines is quite large, with machine 15’s FD cutting being more than 2.5 times higher than that of machine 14. By checking this machine’s single spindle situation from the expert system, it can be seen from Figure 6 that the 10th spindle’s cutting is significantly high, reaching 168.4 times/100 km. We check the yarn passage of this spindle to see if there are any vibrations and whether the clearing device is dusty, using Zippo cleaner for cleaning, then observe the operation, and the cutting returns to normal. The expert system’s daily report allows for quick identification of quality differences in the same variety, and by promptly discovering and addressing these influencing factors, consistency in the quality of the same variety can be ensured.
2.6 Viewing Grading Data and Yarn Defect Cutting Data
Paying attention to the grading and cutting data of various yarn defects, when discovering that individual yarn defect cuts are excessively high or abnormal, timely investigation of the cause is necessary. As shown in Figure 7, the Jp cutting data shows that the group average cutting data is 8.7 times/100 km, but the data for the 18th spindle is very high, reaching 31 times/100 km. Checking the knotting of this spindle reveals that there is a phenomenon of head lifting after knotting. After removing this twisting device, it was found that the rubber damping blocks at the upper and lower clamps were abnormal, with the upper clamp’s rubber damping block damaged and the lower clamp’s rubber damping block missing a corner. After replacing the damping blocks and returning them to the machine, the twisting returned to normal and the Jp knotting cutting was also within the normal range, which greatly assisted equipment personnel in quickly identifying and repairing the issue.
2.7 Viewing Long-term Quality Trends
Long-term quality trend analysis of major quality indicators during the production process ensures that quality differences and fluctuations between batches are controlled. The results of each batch’s cotton blend changes, process changes, etc. can be well displayed in batch reports, facilitating process optimization summaries. Additionally, the filtering function of data reports can be used to analyze and compare quality over different time periods. Furthermore, when there are disputes regarding batch varieties from user feedback, quality traceability can also be conducted.
Key indicators such as output of varieties, cutting yarn defects, average knotting time, number and proportion of locked yarns, downtime, reasons for low efficiency, harmful yarn defects, and quality trends can be collected. As shown in Figure 8, the NSLT cutting trend shows that there were several days with high cutting, especially fluctuations in the cutting of thick knots. The inspection revealed that the fine yarn circulating fan for this variety was damaged, causing fluctuations in yarn quality. As shown in Figure 9, the average knotting time shows that three machines had a higher average knotting time, and upon checking the machines, it was found that several spindles had frequent knotting, resulting in significant differences in knotting. This allowed equipment personnel to promptly maintain the equipment status of abnormal machines, ultimately resolving the quality issue.
2.8 Controlling the Operating Status of Machines
By checking the yarn body situation of the same variety produced by different machines, if there are discrepancies, we check whether the process parameters are consistent. If the differences are significant, the quality variation of the yarn will widen, and the quality differences among yarns will also increase. We once found that a faulty yarn exhibited significant differences in yarn body during use, so we stopped using it. Normal production varieties should exhibit small or nearly identical curves. In addition, based on the distribution of yarn bodies and defects, the best settings can be selected.
Checking whether the joint times of single spindles are balanced, whether the equipment status is good, whether the winding speed meets the set value, and the relationship between winding efficiency and yarn defects and spindle production can effectively improve the production efficiency and quality of the winding process by timely addressing abnormal situations during production. As shown in Figure 10, analyzing the winding efficiency of all produced varieties over a month allows us to see the maximum factors affecting efficiency, facilitating targeted rectifications. Given the large number of varieties, we extract one variety for analysis in the expert system. Figure 11 shows the efficiency analysis of the CF100/2-AX white variety, where the actual efficiency of this variety is 69.5%, with textile alarms affecting efficiency by 3.8%, knotting affecting efficiency by 9.0%, yarn breakage affecting efficiency by 0.5%, and equipment maintenance, cleaning, and downtime affecting efficiency by 17.2%. This allows for data-driven fine analysis of the efficiency of the winding process, leading to insights on the impact of each downtime on winding machine efficiency. Such separate displays of technical alarms, textile alarms, downtime, joint times, and overall downtime aid in problem analysis and diagnosis, facilitating improvement measures and continuously enhancing product quality.
3 Conclusion
The online quality monitoring role of the USTER QUANTUM EXPERT 3 winding expert system has become increasingly important, characterized by intelligence, convenience, speed, and big data operations. Utilizing the data system to analyze the entire production process drives management upgrades in enterprises and effectively improves labor productivity. After a period of use, we have realized that the USTER QUANTUM EXPERT 3 winding expert system ensures simpler control over the winding process, allowing process changes, adjustments, and downloads to be executed synchronously with the USTER QUANTUM 3 electronic clearing device, facilitating changes in machines and process adjustments. Moreover, it is not just data collection; it also helps simplify data processing and guides improvements towards quality goals in all aspects of production, achieving continuous improvement in the production process while maintaining capacity and quality enhancement. The USTER QUANTUM EXPERT 3 winding expert system provides 24-hour online monitoring, with large data volumes covering various aspects of production, processes, quality, and equipment. It is essential to value the application of various data and data analysis, as it not only helps understand yarn quality levels but also identifies issues in various processes, combining charts and alarm information, thereby discovering problems with equipment or individual spindles, creating favorable conditions for rapid diagnosis and timely handling of equipment maintenance. (The author’s unit is: Xinjiang Yida Textile Co., Ltd.)
PS: Comments Editor is ready to respond
(Scroll down to comment and surprises await)
Recent Featured Articles
[Good Luck] After the New Year, I will go into textiles!
[Essentials] Sign management on the workshop floor (can be referenced by textile enterprises)
A textile enterprise suddenly caught fire this morning, the entire factory was basically destroyed. Attached: Causes and response measures for the textile enterprise fire.
Complete guide to factory workshop management
Site management applicable to textile enterprises, personnel, materials, equipment… textile personnel need to understand!
[Ten Years on the Market] How Xinye Textile Builds a “Carrier” for the Textile Industry?
Thanksgiving Day from the perspective of textile personnel, it has gone viral…
Fine yarn falling operation method
In 2017, textile personnel, please remember these seven words!
Trump won: China’s textiles “smiled” while Vietnam’s textiles are going to “cry”!
Complete manual for operation methods of slubbing workers
Textile personnel, please apologize!
Secrets that textile factory managers don’t want to reveal about workshop management comprehensive篇
Chairman Xi presides over the signing of overseas textile project with an investment of 6.6 billion, employing 7,000 workers in the first phase!
What is the biggest waste in textile enterprises?
Another new regulation: the remaining profit margin in textiles… is being squeezed again!
Who will be the “user-trusted product” in 2016 for knitted yarn? Cotton spinning enterprises face a major test on-site?
[Posture] How fine yarn workers combine basic operations to prevent mechanical defects.
[Essentials] Textile personnel must read: Familiarize yourself with safety operation specifications for clearing, cotton carding, slubbing, coarse yarn, fine yarn, etc., to avoid all safety accidents!
Currently, textile enterprises generally face six major difficulties!
The People’s Daily published an article: Who is the “behind-the-scenes hand” pushing cotton prices to soar?
Cotton Textile Technology New Media (WeChat ID: mfzjsxcm)
Reprint must indicate the source
© Cotton Textile Technology New Media (ID: mfzjsxcm)