Toyota recently announced at a technical briefing that it has found excellent materials that may lead to the commercialization of solid-state batteries between 2027 and 2028, launching all-solid-state battery electric vehicles into the market. However, the lack of convincing technical details from Toyota has raised public skepticism.
Solid-state batteries not only have high safety and high energy density, but also exhibit excellent “high and low temperature” performance. These advantages have made them highly anticipated as the next generation of power batteries and a strategic high ground for countries to compete. Thirty years ago, the Oak Ridge National Laboratory in the United States claimed to have developed solid-state batteries, but unfortunately, large-scale mass production has yet to be achieved. In recent years, with the booming global electric vehicle market, several companies have reported progress in the mass production of solid-state batteries, but the news often fades away after being disclosed.
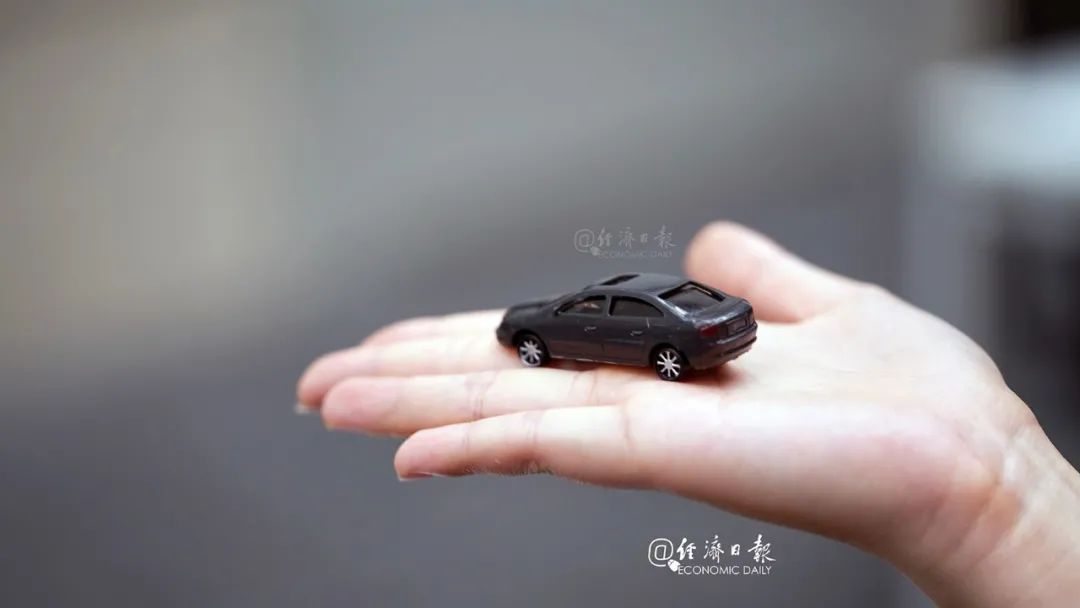
Currently, solid-state batteries can be classified into three technical routes based on material systems. Japanese and Korean companies favor sulfide systems, Europe mainly follows polymer routes, while China focuses on oxides. Among them, Japanese and Korean companies represented by Toyota, Samsung SDI, and Hitachi have significant technological advantages due to their deep technical accumulation and clear trends in collaborative research. However, all three technical routes have fundamental shortcomings that need to be addressed.
Specifically, sulfide electrolytes have poor air stability and produce toxic gases when exposed to air, leading to structural damage and degradation of electrochemical performance. The synthesis, storage, transportation, and post-processing of sulfide electrolytes heavily rely on inert gases or dry rooms. Polymer electrolytes have low ionic conductivity at room temperature, requiring high-temperature environments for charging, which severely limits their commercialization. Most oxide electrolytes have a wider electrochemical stability window and better oxidation stability, but to ensure good contact between rigid oxide electrolytes and cathode materials, high-temperature sintering is often necessary, otherwise serious interfacial chemical side reactions may occur. Additionally, some oxide electrolytes face lithium dendrite growth issues.
At the same time, cost is also a significant hurdle for companies. Currently, the cost of semi-solid batteries is much higher than that of commercial liquid batteries. According to industry research and estimates, taking NCM811 liquid cells and NCM811 semi-solid cells as examples, the cost of semi-solid cells is approximately 80% higher than that of liquid cells. Among these, the cost of solid electrolytes is the main additional cost, accounting for about 50% of the total cost of semi-solid batteries. Factors such as changes in electrolyte material, alterations in production processes, and insufficient experience in product quality control lead to longer engineering verification cycles, making full solid-state batteries even more expensive than semi-solid batteries.
To evaluate whether a power battery can be mass-produced, there are mainly five indicators: energy density, charge-discharge rate performance, cost, safety, and cycle life. Laboratory research results for power batteries generally achieve significant breakthroughs in one or several indicators at certain stages, and it is only possible to mass-produce if all five indicators are met. In other words, based on the current R&D progress of major companies, while solid-state batteries seem to be on the verge of a breakthrough, the actual path is fraught with challenges and mass production remains quite difficult.
Compared to structural innovations, improvements in battery materials are indeed slower and more challenging. However, difficulty does not mean we should not pursue it; as we often say, it is wise to do “difficult but correct things.” From the perspective of technological transformation, the innovation of power battery technology plays a leading role in the development of electric vehicles. The reason why China’s new energy vehicle industry can lead globally is that we have made breakthroughs in power batteries, giving rise to global power battery giants like CATL.
In the industrial transformation driven by the “dual carbon” goals, innovation in power batteries has become key in enhancing the competitiveness of new energy vehicles, building national industrial competitiveness, and solidifying corporate competitive advantages. Whether it is a pioneering country in new energy vehicles or a follower, or any enterprise within the power battery supply chain, all are targeting new technologies and laying out solid-state batteries. This presents both a significant challenge and a rare opportunity. The advantages of a super-large market, leading full-industry competitiveness, and continually rising innovation capabilities put China in a better position to seize the strategic high ground of power batteries.

Source/Economic Daily (Author: Yang Zhongyang)
Supervised by/Zhang Yiyong
This content is original; please indicate the source when reprinting.
If you find it interesting, please click “See More” ↓↓↓