Click the above “Beginner’s Guide to Vision“, select to add “Starred” or “Pinned“
Heavy-duty content delivered in real-time
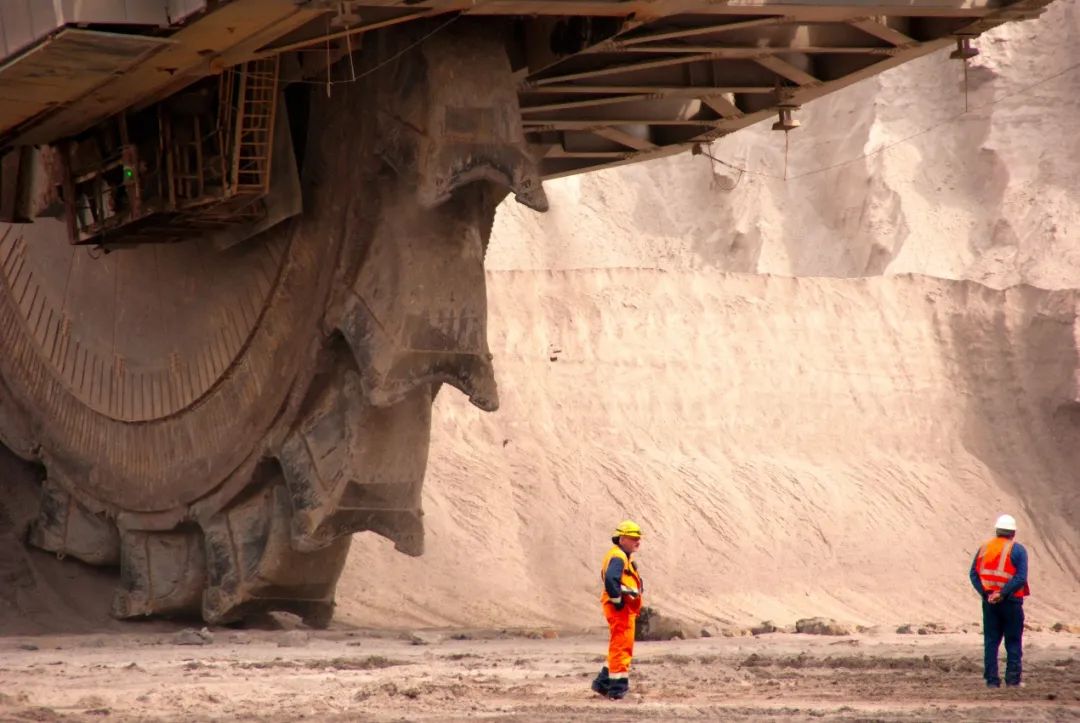
Computer vision is a technology that analyzes images (including videos) through computer systems. An increasing number of image processing algorithms facilitate the application of computer vision in autonomous driving, industrial robotics, and related fields.
The mining and processing of natural resources have become increasingly complex, involving operations in extremely harsh conditions. Whether mining coal several kilometers deep or drilling oil wells underwater, workers face significant risks, making it preferable to replace manual labor with machines in hazardous conditions.
Using artificial intelligence (AI), this goal can be achieved. Industry 4.0 signifies a transition to fully automated digital production, a process controlled in real-time by intelligent systems while continuously interacting with the environment. At the core of this concept is the creation of a “digital” that refers to the digitization of actual physical assets. The prerequisite for implementing Industry 4.0 is the installation of sensors to collect and analyze data about processes. Cameras are among the best sensors, as computer vision systems can obtain visual representations of real objects, process them, and analyze them later to address various application tasks.
CV has many practical applications in industry, from product quality control on production lines to safety monitoring, among others. Here are some of the most common industrial case studies in the field of computer vision.
01.Production Quality Control
The results of manual visual inspections largely depend on the operator’s ability, experience, and concentration. This labor-intensive process can lead to issues such as missed defects or misclassifications. To reduce human influence and improve the accuracy and reliability of quality control processes, computer vision systems can be employed. There are primarily two detection schemes: control of semi-finished products and inspection of finished products. Using neural networks, it is possible to detect 92%-99% of defective products, with false positives accounting for 3-4%. Such performance ratios make it feasible for computer vision to replace human labor.
Missed defects can lead to very serious problems, which is why many are researching this situation. In addition to visual analysis, there are other non-destructive testing methods, such as ultrasound, eddy current, and X-ray control. Information about the temperature and geometric data of the object’s surface can also be used in addition to traditional cameras.
Modern computer vision systems can identify potential hazardous situations for industrial assets. By tracking events according to specified parameters, the occurrence of hazardous incidents can be minimized, ensuring continuous operation of equipment and reducing the risk of workplace injuries. By using data from cameras and other sensors in the production area, safety for workers can be significantly improved.
This includes monitoring the wear of personal protective equipment (helmets, safety cables, work clothes, headsets) and the presence of personnel in hazardous areas. This solution can automatically detect violations and provide reasonable feedback to personnel, thereby fostering safe working habits. If someone enters a hazardous area, an alarm is triggered.
Through video analysis, open flames, pipeline ruptures, leaks, identifying broken fences, or any attempts to remove items from the protected area and detect abandoned objects can also be detected. In certain areas (such as gas stations), the use of smokers or mobile phones can also be tracked. Additionally, fatigue detection can be performed. This system tracks employees’ activities to improve task allocation management.
Computer vision is used to monitor production facilities and infrastructure. The range of video analysis capabilities includes detecting and locating moving objects, vehicles, and the positions of equipment and personnel. It can identify and track various activities with precision beyond human capabilities. Based on this monitoring, intelligent task allocation can enhance productivity and increase overall equipment utilization.
In every stage of the logistics process, calculate and estimate pipeline sizes.
Mining now allows us to classify, count, and estimate the size of moving ore blocks during the mining and transportation processes. Rock fragment analysis enables adjustments to blasting operations. Such systems have improved process productivity by 3-4%. Optical granulometers provide real-time insights into completed work. A relevant task is to monitor the rubble on conveyor belts to detect anomalies in crushing and sorting plants.
The estimated size of ore fragments fed into equipment for subsequent processing can automatically adjust the crusher’s mode and achieve optimal yield. Systems designed to automatically classify rock types after drilling assist in faster and more accurate identification of discovered mineral collections than humans.
There are also monitoring systems that can determine the presence of bucket excavator teeth in real time. Losing just one bucket tooth can reduce an excavator’s productivity by about 1.3%. Moreover, if a tooth reaches the crusher, it can cause damage and downtime, amounting to $8,000 per hour, excluding search and repair costs. In cases of loss and damage, audio signals to the operator can minimize these negative impacts.
Using Drones to Enter Hazardous Areas: Companies use drones to monitor their assets and operations, quarries, and dams, and detect leaks in pipeline infrastructure. There is also a solution for analyzing the structure and conditions of abandoned underground mines to control subsidence and water pollution under unsafe conditions. With this technology, geotechnical engineers can better reconstruct mine maps and safely monitor their current status.
In metallurgy, computer vision has the potential to control quality, determine the microstructure and mechanical properties of alloys, and search for new materials with desired characteristics. It has been shown that machine learning and expert involvement can perfectly address the tasks of alloy evaluation.
The design and development of materials from initial discovery to commercialization have historically taken decades. By using stored laboratory data, computer vision can discover materials, design, and predict their performance. Since grain structure affects steel cracking, visualizing cracks can link macro-mechanical and microstructural characteristics to predict crack propagation paths.
Defect detection technologies in metallurgy have their unique properties, requiring the use of additional analytical tools beyond traditional cameras. For instance, surface temperature assessments through color analysis can reveal the extent of harmful mineral contamination and the conditions of processes or reactors. Specifically, neural networks have been successfully trained to identify perlite, ferrite, martensite, and cementite.
Over the past few decades, industrial robots have nearly replaced manual labor in capturing and handling different objects. The first models of industrial robots were designed to perform simple tasks. Now, robots and collaborative robots can reposition objects using grippers or vacuum cups. They paint, bend wires, perform spot welding, and execute other routine operations. Modern robots equipped with computer vision systems can perform tasks characterized by significant variations in workpiece positions.
Robots have been used in industry for a long time, but AI has only just begun to penetrate this field. Historically, GPU computing for industrial applications is a relatively new area, and industrial computer vision involves a range of sensors, not just video streams. Robots with computer vision systems can consider object positions by analyzing video streams from 3D cameras and data from lasers and sensors. This approach allows robots to execute tasks with high precision under almost any conditions.
Robots with computer vision require less programming. They only need to be configured once before starting. Additionally, robots can switch tasks seamlessly with minimal downtime. Due to their high flexibility and minimal programming needs, computer vision robots can effectively complete tasks without knowing the exact parameters of the parts. The adaptability of robots allows them to select the required parts, localize them, and classify them from any position. A minimal investment in equipment setup is one of the most apparent benefits.
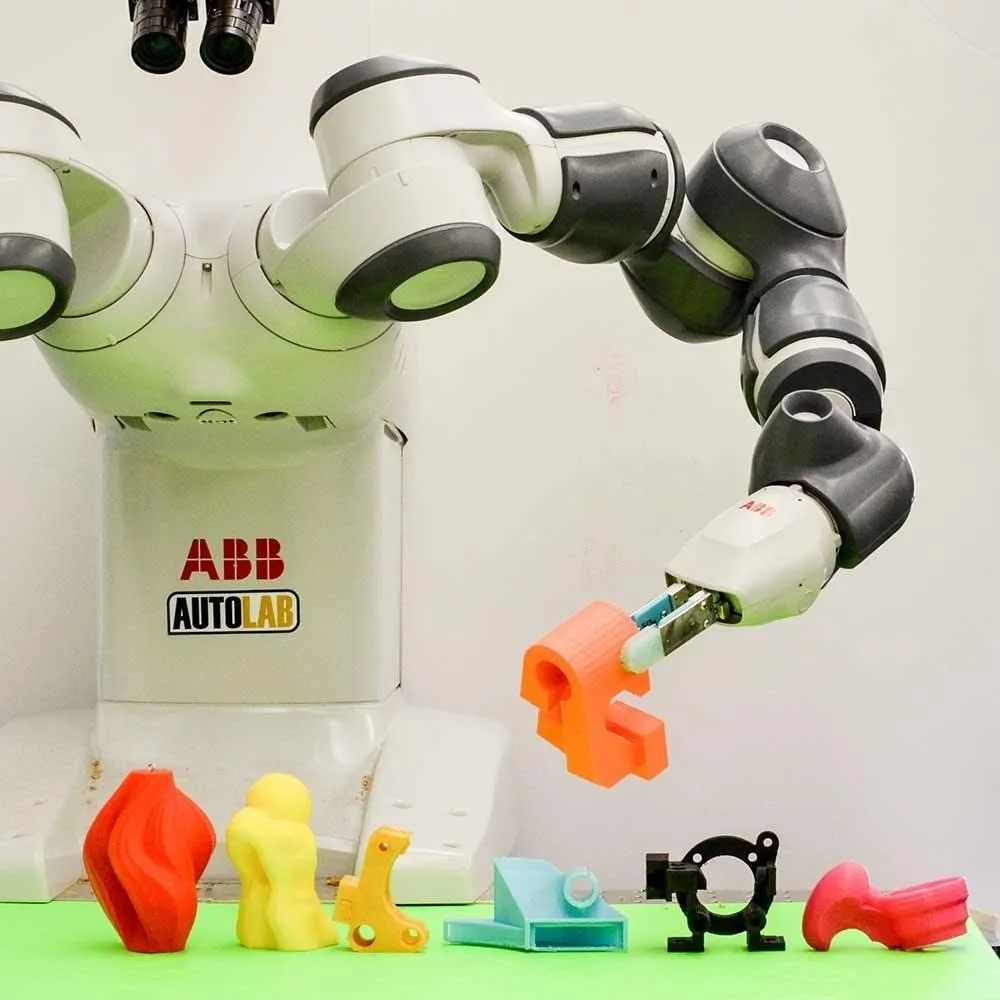
Using the Dex-Net 4.0 algorithm to capture variable items
Dex-Net 4.0 is a robot with an arm that can grab objects with astonishing precision. It can capture up to 300 objects per hour with a 95% success rate. It evaluates several options to capture an object within seconds. Humans can capture 400 to 600 objects per hour. Computer vision continues to expand the capabilities of industrial robots and find new ways to improve productivity in routine tasks.
With the development of e-commerce, logistics robots have become a promising area of robotics. They serve in goods delivery and collaborate with humans. They can transport loads of up to 15 kilograms, navigate in challenging conditions, and maneuver effectively between people. Autonomous mobile robots can operate without supporting infrastructure such as markers, wires, magnets, or precise target positioning. They enhance production efficiency and reduce costs, making them an essential component of production environments. Warehouse robots have enabled Amazon to reduce operational costs by about 20% per warehouse (saving approximately $22 million annually). According to the McKinsey Global Institute (MGI), the cost savings across the industry due to various automation operations could range from 15% to 90%, depending on the sector.
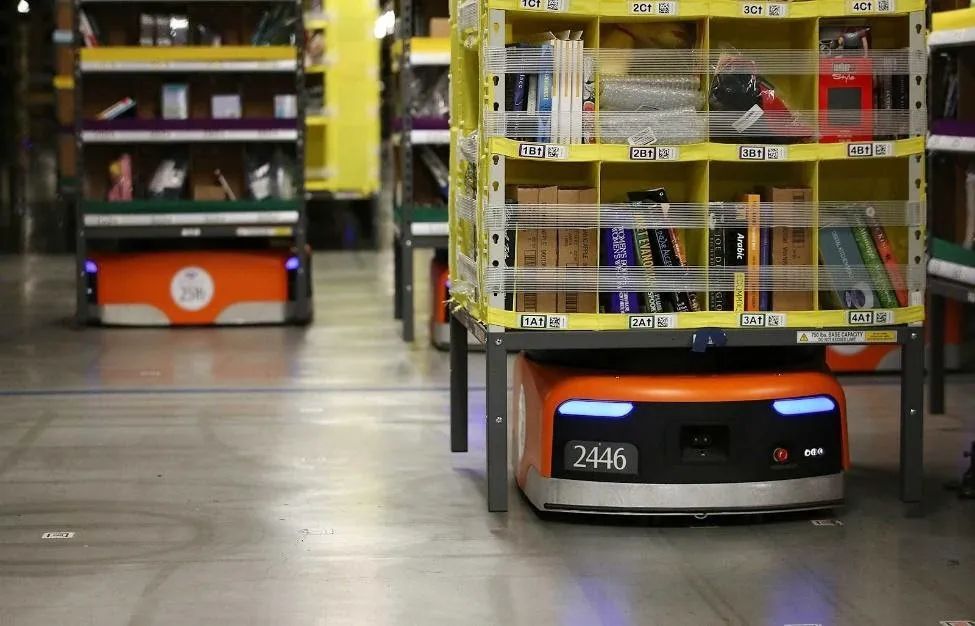
Amazon warehouse robots
When planning robotic manipulation, computer vision will be used to avoid collisions. The data source for the algorithm is the laser radar installed on the robot. Objects are first detected, followed by motion tracking. Robots need to understand their environment and predict the movements of others, which is essential when moving in a constantly changing environment. Navigation and obstacle avoidance; remembering and considering the path of travel and positioning themselves in space—all these tasks can be solved using principles of computer vision.
Several types of logistics robots already exist, as well as complex solutions for automating warehousing, including industrial robotic arms, mobile robotic trolleys, and stackers. Boston Dynamics launched its new Handle robot loader in March. They are faster than forklifts and can sort items in pallets and transfer storage units to conveyor belts. Each of these two-wheeled balancing robots is equipped with a mechanical hand and vacuum handle, along with a computer vision model that allows it to navigate warehouses and select the required shelves and boxes. Advanced computer vision and grippers will expand the application range of logistics robots.
Boston Dynamics Handle robot
Discussion Group
Welcome to join the public account reader group to exchange ideas with peers. Currently, there are WeChat groups on SLAM, 3D vision, sensors, autonomous driving, computational photography, detection, segmentation, recognition, medical imaging, GAN, algorithm competitions, etc. (these will be gradually subdivided). Please scan the WeChat ID below to join the group, with a note: “nickname + school/company + research direction”, e.g., “Zhang San + Shanghai Jiaotong University + Vision SLAM”. Please follow the format, otherwise, you will not be approved. After successful addition, you will be invited to relevant WeChat groups based on your research direction. Please do not send advertisements in the group, or you will be removed from the group. Thank you for your understanding~
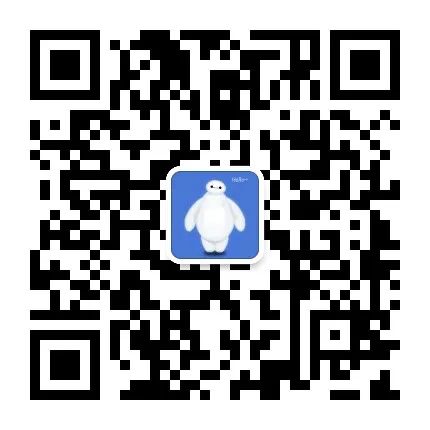
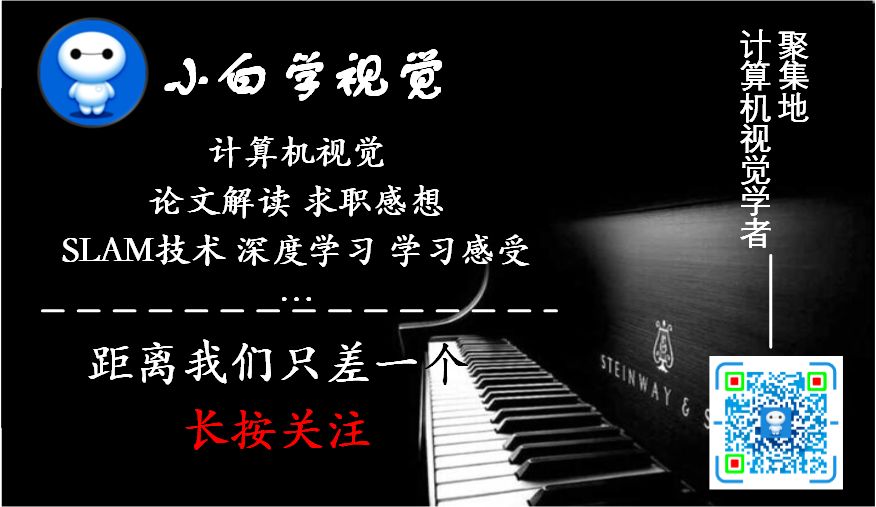